The applications of the
Power-D Manufacturing series saw the light as a result
of experience acquired on different types of production plants and processes;
AST system automation has been engaged in ongoing research aimed at providing
manufacturing industries with the tools required to tackle the current situation
of market hyper-competitiveness.
The growing demand for flexibility and innovative products obliges manufacturing companies to speed up the evolution of their production processes
(flows, machines and plants). Moreover, the increasing reduction of operating margins highlights a greater need for more efficient organisations,
with a more harmonic and dynamic contact with the production process to ensure this is increasingly more
in line and perfectly consistent with the demands of the market and individual
customers.
What is required is a “slim organisation” able to gradually involve existing staff and plants so
as to achieve ongoing improvement of performance and adaptation of products to market demands,
with the primary aim of maintaining and upgrading corporate profitability.
AST system automation offers solutions that permit and facilitate a change in the approach
to solving daily problems, real added value of our actions,
to focus attention on the results of the quality provided and released after doing a job.
Available products are:
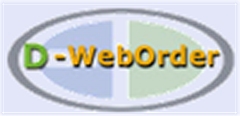 |
D – WebOrder (Order execution management via Web)
Web application for placing and tracking orders via the Web.
|
 |
|
D – TRACK (Machine state traceability)
System for the smart tracing of machine operating and stop states, with results shown through the company’s ethernet network.
|
 |
|
D-LINE manager ( Automatic set-up of machines without stopping the production flow)
Specific system for the immediately changing the production set-up,
to adapt to a new type of product without stopping the machine; to be fitted on existing machines, systems and lines already existing.
|
 |
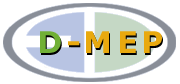 |
D-MEP
(Production Efficiency monitor)
Web application that permits collecting up all the production facility data to monitor the
production efficiency of the machines and workforce. |
 |
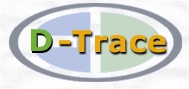 |
D-TRACE
(Process Product Data Traceability)
The Web application for collecting and historicizing all the Data Relating to Machining Operations and Products that have gone through the Production Process, pursuant to ISO-9001 and regulations on Product Traceability. |
|
|
D-STORE
(Product handling management with automatic stores)
Software package for managing automatic stores. Allows creating and cancelling missions from and to the store, optimising the launch of missions, updating stocks and communicating with the PLCs.
|
 |
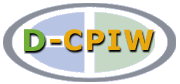 |
D-CPIW
(Production process coding and sharing of corporate know-how)
Specific application for the Digital Configuration and Coding of the production process.
Departments, Production Lines, Machines and Components can be coded in detail and split up by areas,
sub-areas, positions and elements. All existing documentation is filed in an organised way and in digital format.
Also permits monitoring the state of the Variations and Modifications made during the entire life cycle of
the instrumental asset and keeping this updated.
|
 |
|
D-MP (Machines and systems maintenance management)
Web application for managing all the Personnel/machinery “interactions”
(operators and maintenance technicians). It also controls and stores all the maintenance activities of the facility.
|
 |
Our intervention guidelines are:
Implementing production facility flexibility:
A situation has to be created in which operators are safer, more precise and faster in regulating and adapting
the machines to the new type of product to be made.
Moreover, a standardised and always more specific parameterisation of the production process,
able to enter into the smallest detail and shared between several people, results in cutting set-up and tuning times.
The cutting of set-up times can be operatively pursued by implementing an upgrade programme centred
not only on acquiring new cutting-edge technology plants, but also by the organisational upgrading
of the technologies of existing plants by means of simple interventions distinguished by high technological efficacy.
Such interventions require the direct involvement of the production and maintenance departments.
Constant maintenance of production pace and performance
measuring:
A major aspect for production efficiency is to identify wastes,
weak points of the structure, any bottlenecks that slow down the production flow,
in order to take action and make possible continuous upgrading that maintains
the production process at a constant pace.
The frenetic pace of production changes requires the adoption of a dynamic data detection
system so as to be able to assess both the product and the process and at the same
time immediately identify the points where either the product or the process are no longer profitable.
(By dynamic system is meant that the user can easily adapt and configure the changes made).
This is a period in which the difference is made above all by increasing the performance
of assets in terms of operating availability, plant and line efficiency,
reduction of costs and quality defects; but it is above all through the optimisation of
plant use that it becomes possible to increase value added.
Experience management and sharing among people:
We are all aware that good results derive from the technical, organisational and psychological
skills of the people who work inside the facility.
Providing knowledge "fertility" conditions and ensuring compatibility with
corporate strategies is the cultural challenge to be taken up every day.
In view of the growing difficulty in processing production process data, people must be helped to manage the data relating both to highly complex existing systems and to any future systems yet to be acquired.
Ongoing technological developments produce increasing more complicated and sophisticated machinery which, in case of faults, can only be attended to by skilled engineers.
The operator, the maintenance technician and the process engineer are the only people
who live regularly in contact with the machines and experience all their positive and negative aspects;
allowing the engineers to offer suggestions relating to the problems found in any easy,
fast and practical way without a lot of red tape, permits subsequently transforming this
information into a reusable resource.
Maintenance and other jobs aimed at ongoing improvement:
To avoid downtimes, malfunctions must be remedied before they occur.
To adapt to change, concrete modifications must be made that tend to eliminate wastes.
Possible goals and results for the customer
- correct use of machine and system data and information
(create a uniform procedure for using and managing the data relating to plants and equipment)
- increase of system operating availability
(production efficiency: an increase of 5-10% is expected within a period of 2-3 years)
- cut in production costs
- capacity to "measure" the efficiency and the effectiveness of production plants
(monitoring of significant data per single machine, island, or production line)
- upgrading personnel training
(to make the personnel more responsible for production performance and foster awareness of the importance of the single parts of plants and equipment)
- rationalisation of fixed assets in spare parts
(more rapid response and solution of machine down times due to breakdowns)
- control of production evolution and process
(crucial requisite for monitoring ongoing improvement, maintaining set goals and checking costs with work in progress)
|