Los aplicativos de la familia
Power-D Manufacturing nacen de una experiencia madurada en diferentes tipos de instalaciones y de procesos productivos; AST system automation ha llevado a cabo un constante trabajo de investigación, finalizado a proporcionar a las industrias manufactureras los instrumentos adecuados para hacer frente a la actual situación de hiper-competitividad del mercado.
La creciente necesidad de flexibilidad y de ofrecer productos innovadores impone a la empresa manufacturera una forzada evolución del proceso productivo (flujos, máquinas y equipos).
Así mismo, la creciente reducción de los márgenes operativos evidencia la necesidad de hacer la estructura más eficiente, creando un contacto más equilibrado y dinámico con el proceso productivo, con la finalidad de hacerlo cada vez más acorde y en perfecta sintonía con las exigencias del mercado y de los clientes.
Se trata, en definitiva, de crear una estructura organizativa ágil que ataña gradualmente a las personas y a las instalaciones existentes, con el objeto de obtener una mejora continua de las prestaciones así como de adaptar los productos a las necesidades del mercado, para mantener y mejorar la rentabilidad de la empresa.
AST system automation ofrece soluciones que posibilitan y agilizan el cambio necesario para solucionar las problemáticas cotidianas, verdadero valor añadido de nuestras acciones, para focalizar la atención de la calidad prestada y ofrecida tras una intervención.
Estos son los productos disponibles:
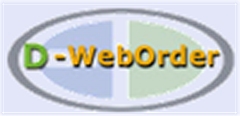 |
D – WebOrder
(Gestión avance pedidos vía Web)
Aplicativo Web que permite efectuar pedidos vía Web y seguir el avance de la producción.
|
 |
|
D
– TRACK (Trazabilidad de los estados máquina)
Sistema que permite una inteligente recogida de los estados de funcionamiento y de parada de las máquinas, evidenciando los resultados a través de la red ethernet de la empresa.
|
 |
|
D-LINE manager
(
Set-up automático de las máquinas sin parada del flujo productivo)
Sistema específico para el cambio de set-up al vuelo de la producción, que permite la adaptación al nuevo tipo de producto sin la parada de las máquinas, y que puede aplicarse en máquinas, instalaciones y líneas existentes.
|
 |
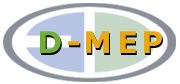 |
D-MEP
( Monitor Eficiencia Productiva)
Aplicativo Web que permite la recogida de todos los datos del establecimiento para poder monitorizar la eficiencia productiva de las máquinas y de los hombres.
|
 |
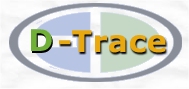 |
D-TRACE
( Trazabilidad de los Datos de los Productos en el Proceso)
El aplicativo Web que permite la recogida y la realización del historial de todos los datos concernientes a los tratamientos y a los productos que han pasado por el proceso productivo, de conformidad con la norma ISO-9001 y con la normativa sobre la trazabilidad de los productos.
|
|
|
D-STORE
(Gestión desplazamiento productos con almacenes automáticos) Paquete software para la gestión de almacenes automáticos. Permite crear y borrar misiones desde y hacia el almacén, optimizar el lanzamiento de las misiones, actualizar las existencias y comunicar con los PLC.
|
 |
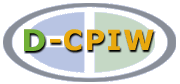 |
D-CPIW
(Codificación del proceso productivo y participación en el Know-how empresarial)
Aplicativo específico para la Configuración y Codificación Digital del proceso productivo. Se codifican hasta en los más mínimos particulares Secciones, Líneas de producción, Máquinas y Componentes, divididos por zonas, subzonas, posiciones y Elementos. Se archiva de modo estructurado y en formato digital toda la documentación existente. Permite monitorizar y tener actualizado el estado de las Variaciones y Modificaciones aportadas a lo largo de todo el ciclo de vida del bien instrumental.
|
 |
|
D-MP (Gestión Mantenimiento máquinas e instalaciones)
Aplicativo Web para la gestión de todas las interacciones del Personal con las máquinas (los Conductores y los Técnicos de Mantenimiento), así mismo gestiona y memoriza todas las actividades de mantenimiento de un establecimiento.
|
 |
Las líneas guía de nuestra intervención son las siguientes::
Implementar la flexibilidad en el establecimiento:
Es necesario crear una situación en la que los empleados puedan estar seguros y ser más precisos y rápidos en la regulación y en la adaptación de las máquinas al nuevo tipo de producto que se ha de producir.
Del mismo modo, una parametrización estandarizada y cada vez más específica del proceso productivo, capaz de entrar en los más mínimos detalles y compartida por varias personas, permite reducir los tiempos de set-up y de puesta a punto.
La reducción de los tiempos de set-up puede obtenerse operativamente a través de un programa de mejora, finalizado no sólo a la adquisición de nuevas instalaciones tecnológicamente avanzadas, sino también a la mejora organizativa de la tecnología de las instalaciones existentes mediante simples intervenciones de gran eficacia tecnológica.
Dichas intervenciones requieren la implicación directa de los sectores de producción y de mantenimiento.
Mantenimiento constante del ritmo productivo y cuantificación de las prestaciones
Un aspecto importante a fines de la eficiencia productiva es poder localizar los derroches, los puntos débiles de la estructura y los posibles obstáculos que ralentizan el flujo productivo, para poder así intervenir y posibilitar una mejora continua que mantenga el proceso productivo a ritmos constantes.
El ritmo frenético de las variaciones productivas requiere la adopción de un sistema dinámico de detección de los datos, de modo que se pueda valorar tanto el producto como el proceso, y que permita evidenciar inmediatamente los puntos en los que el producto o el proceso ya no son rentables.
Por tanto, un sistema dinámico significa que el usuario puede adaptar y configurar fácilmente las modificaciones aportadas.
En la era en la que vivimos la diferencia se crea aumentando las prestaciones de los assets en términos de disponibilidad operativa, de eficiencia de las instalaciones y de las líneas, y de reducción de los costes y de los defectos de calidad; del mismo modo, para generar un incremento del valor añadido es imprescindible una optimización de la utilización de las instalaciones.
Gestionar y compartir la experiencia
Hoy, es un dato de hecho que los buenos resultados derivan de las competencias técnicas, organizativas y psicológicas de las personas que trabajan en la empresa.
Predisponer condiciones de "fertilidad" del conocimiento y garantizar su compatibilidad con las estrategias empresariales es el reto cultural que hay que superar día a día.
Frente a la creciente dificultad del tratamiento de las informaciones concernientes al proceso productivo, es necesario dar facilidades para que las personas gestionen dichas informaciones relativas tanto a una instalación ya existente muy compleja, como a un sistema que se quiere adquirir.
La continua evolución tecnológica propone maquinarias cada vez más complicadas y sofisticadas, que en caso de anomalía requieren la inmediata intervención exclusivamente de técnicos especializados.
El conductor, el técnico de mantenimiento y el ingeniero de proceso son las únicas personas que viven constantemente en contacto con las máquinas y que conocen todos los aspectos, tanto positivos como negativos, de las mismas. La posibilidad de que los técnicos indiquen las problemáticas detectadas de modo ágil, rápido y práctico, sin burocratizar los procedimientos, permite transformar sucesivamente estas informaciones en recursos reutilizables.
Mantenimiento e intervenciones finalizadas a la mejora continua
Para evitar paros en las instalaciones es sumamente importante poder anticipar los posibles fallos de funcionamiento.
Para adaptarse al cambio hay que efectuar modificaciones concretas finalizadas a eliminar los derroches.
Objetivos y resultados posibles para el cliente:
- Utilización correcta de los datos y de las informaciones de las máquinas y de las instalaciones.
( crear una modalidad uniforme para la utilización y la gestión de los datos de los paros técnicos)
- Aumento de la disponibilidad operativa de las instalaciones.
(eficiencia productiva: se prevé un aumento del 5-10% en el arco de 2-3 años)
- reducción de los costes de producción
- Capacidad de "medir" la eficiencia y la eficacia de las instalaciones productivas.
(monitorización de los datos significativos para cada máquina, isla o línea de producción)
- Mejorar la formación del personal.
(responsabilizar más al personal sobre el rendimiento de la producción y sobre la importancia de cada parte de los paros técnicos)
- Racionalización de los paros en piezas de recambio.
( aumento de la rapidez de respuesta y resolución de los paros máquina debidos a averías)
- Control de la evolución y del proceso productivo.
(requisito fundamental para monitorizar la mejora continua, mantener los objetivos previamente establecidos y comprobar los costes durante todo el proceso)
|